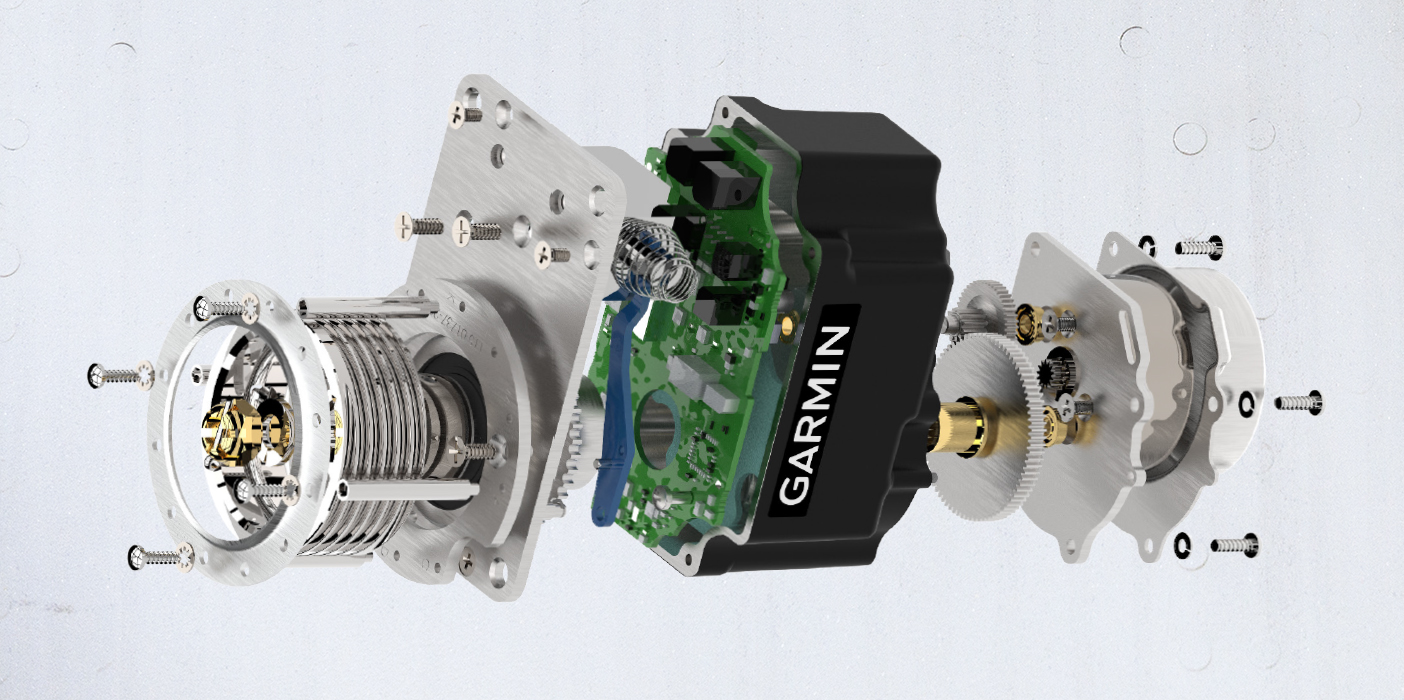
GFC 500 & GFC 600—Safety-Enhancing, Cost-Reducing Technology
Autopilots have been around nearly as long as aircraft themselves. For decades, they have been assisting pilots by reducing workload on long flights and helping to precisely navigate approaches. The fundamental concept of an autopilot remains the same: to automatically provide pitch, roll and yaw forces without the pilot touching the flight controls. What’s changed in the time since the first modern autopilot is the system itself — how it works and the hardware it uses to generate those pitch, roll and yaw forces. Our engineers have reimagined the general aviation autopilot system using modern technology plus design elements from our GFC 700 autopilot, a popular solution found in thousands of business aircraft, and created the GFC 500 and GFC 600 digital autopilots available for retrofit on thousands of general aviation aircraft.
A motor with enhanced reliability, lower operating costs
The autopilot’s automatic control inputs are carried out by servo motors installed alongside an aircraft’s control surface mechanisms. Traditionally, these servos are powered by brushed motors—designs powered through brushes with a tendency for contact wear over time. Because of this anticipated wear, servos require regular maintenance or overhaul intervals—sometimes as little as every few hundred hours costing thousands of dollars.
In order to improve the long-term performance, reliability and operating costs of our autopilots, we designed the servos for our GFC 500 and GFC 600 with brushless DC motors. These contactless motors result in a powerful servo with fewer inspection requirements, reduced maintenance costs, and aircraft downtime.

Smart technology in a smart servo
Traditional autopilot servos typically contain fail-safe design elements such as a mechanical slip clutch or shear pin to ensure pilots can always overpower an autopilot and take control of the aircraft. A variety of factors, including fatigue, can cause a shear pin to break, necessitating a repair. While mechanical slip clutch and shear pins are in place for fail-safe purposes, they can require constant adjustment or repair.
In our GFC 500 and GFC 600 autopilot servos, we eliminated the need for mechanical slip clutches and shear pins altogether. Instead, our servos incorporate a feature that decouples the motor drives when the autopilot is turned off or disengaged, providing virtually no control system friction. That way, pilots can easily hand-fly or override the system without fighting the controls. And, each servo is monitored by its own built-in microprocessor, providing the “smart” logic to significantly improve sensor performance, response and self-monitoring capabilities. A truly smart, digital solution with potentially safety-enhancing and cost-reducing benefits in the long run.
A growing Approved Model List (AML)
The approved model lists for the GFC 500 and GFC 600 continue to grow. To date, dozens of legacy aircraft are eligible for these retrofit autopilot solutions. The GFC 500—tailored for light single-engine piston, fixed-wing aircraft—is ready to be installed on many popular Cessna, Beechcraft, Piper aircraft and more. The GFC 600—designed for higher-performance single- and twin-engine piston and turbine aircraft—is available for select Cessna and Beechcraft aircraft, with many more coming soon.
For more information about the GFC 500 and GFC 600 autopilots, visit our website at garmin.com/aviation.